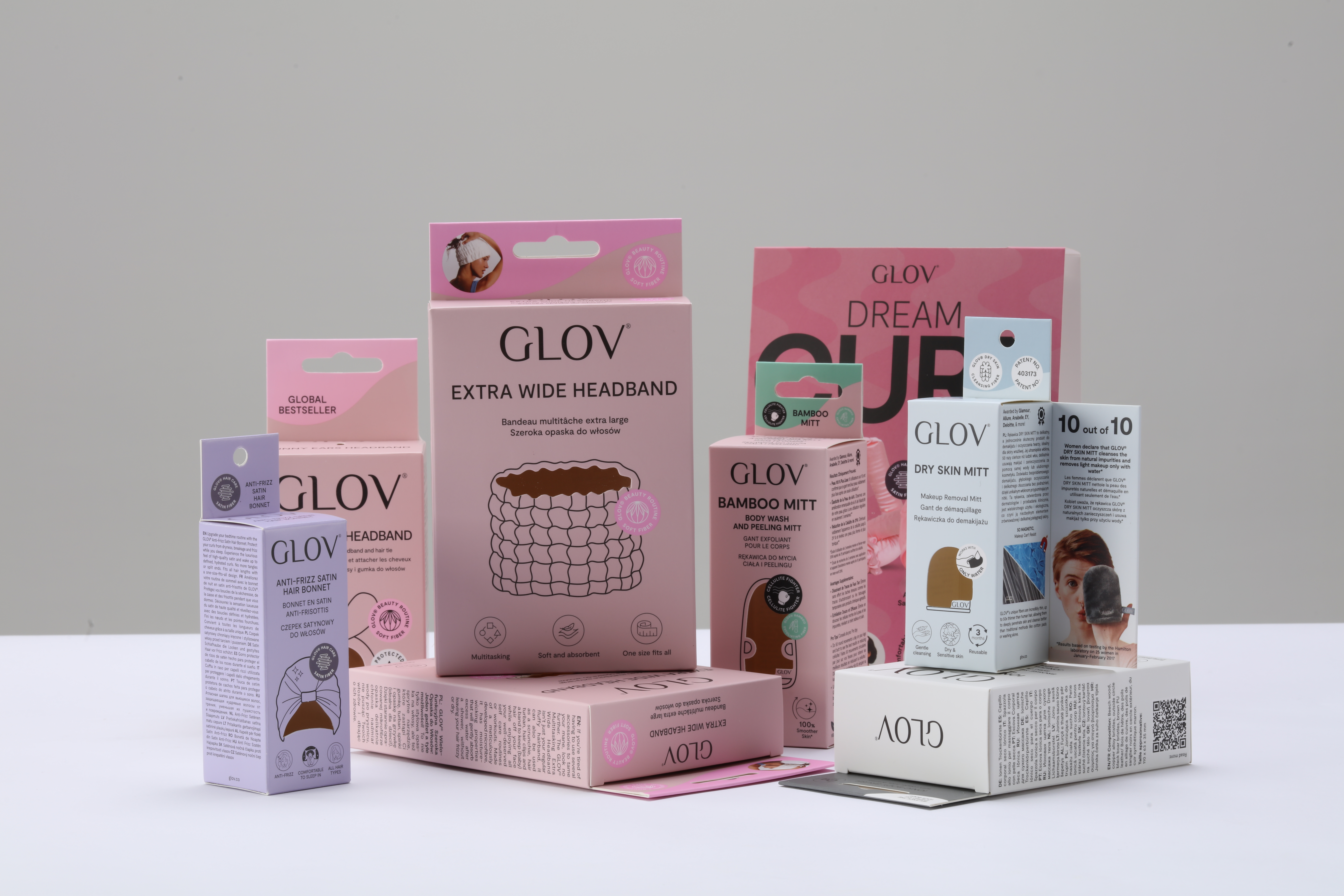
Providing samples to customers for confirmation before paper box products enter mass production (bulk production) is a crucial link in the packaging industry (especially customized production). The main reasons include the following:
1. Confirm the consistency between the design and customer needs
Avoid misunderstanding: The design documents provided by the customer (such as size, structure, printing content, etc.) may have errors when converted into actual samples (such as color deviation, dimensional accuracy, folding method, etc.). Samples are the key to physical verification, ensuring that both parties have a completely consistent understanding of the design intent.
Functional testing: Customers may need to test the actual use performance of the cardboard box, such as load-bearing capacity, stacking stability, and opening and closing convenience. Samples are the core basis for verifying functions.
2. Ensure that the printing effect and material meet the requirements
Color accuracy: Printing colors (such as Pantone color numbers) may differ in screen display, design drafts, and actual printing. Samples allow customers to confirm whether the color meets brand standards.
Material verification: Paper weight, surface treatment (such as matte, bright film, hot stamping, etc.), environmental certification, etc. need to be confirmed through physical samples to avoid customer rejection due to the use of wrong materials in bulk goods.
3. Reduce the risk of mass production
Cost control: Paper boxes are usually produced in large quantities. Once there is an error in the mass production (such as design errors, process defects), the cost of rework or redoing is extremely high (involving materials, labor, and time). Sample confirmation can put the problem in front and reduce risks.
Time guarantee: If problems are found after the mass production, it may delay the customer's product launch plan (such as holiday gift boxes miss the sales schedule). Correction at the sample stage can avoid such losses.
4. The need for internal customer processes
Multi-department collaboration: Customers may need to submit samples to the marketing department, quality inspection department or end users (such as brands) for review, or even for consumer testing (such as packaging experience research).
Compliance review: Some industries (such as food and medicine) need to verify whether the packaging meets safety standards (such as moisture resistance, food-grade ink certification), and samples are necessary materials for submission to regulatory authorities or third-party testing.
5. Legal and contractual basis
Clear acceptance standards: After the sample is signed and confirmed by the customer, it can become a reference standard for subsequent mass acceptance to avoid disputes caused by vague quality standards.
Responsibility division: If the bulk product does not match the sample, the responsibility is clear (if the supplier does not produce according to the sample, it must bear compensation).
6. Optimize production process
Process feasibility verification: Some complex structures (such as special-shaped boxes, special window designs) may expose production difficulties (such as die-cutting accuracy, bonding strength) during the proofing stage, and suppliers can adjust process parameters in advance.
Efficiency improvement: Through sample testing, the production process can be optimized (such as reducing waste and adjusting the sequence of processes), which can reduce costs and increase efficiency for bulk production.
7. Build trust and long-term cooperation
Professionalism: Proactively providing samples shows that the supplier pays attention to details and enhances customers' confidence in production capabilities.
Quick response to needs: If customers propose modification suggestions (such as adjusting the LOGO position and adding anti-counterfeiting labels), the modification cost at the sample stage is much lower than that at the bulk stage.
Post time: Apr-08-2025